A Tenant of Kalibr Technopark has Patented an Endoprosthesis of the Wrist Joint for Maintaining the Mobility of Hands
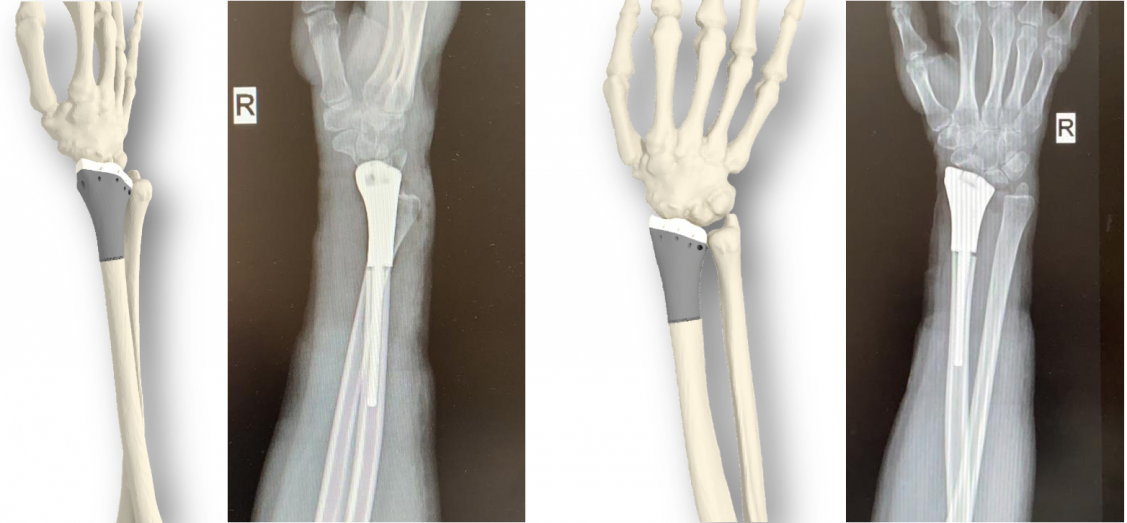
Titanium implants for the replacement of the affected bone areas are printed on a 3D printer and accurately replicate the individual characteristics of the patient. The unique technology allows you to fully maintain the mobility of the hands and their ability to rotate.
The Tenant of Kalibr Technopark - the Endoprint Innovative and Technological Company - has patented a new unipolar endoprosthesis of the wrist joint. The development allows you to replace the affected area of the bone and joint while maintaining full mobility of the hand. The product is designed taking into account the individual characteristics of the joint and bone canals of a particular patient and printed on a special 3D printer made of titanium.
«Most of the residents of technoparks are engaged in the development of complex technological products that require special equipment. The city provides an opportunity to reimburse the costs of its acquisition, leasing or purchase on credit, as well as interest on loans for business development. Companies can receive up to 10 million rubles by submitting an application during the application period, '' said Alexei Fursin, head of the Moscow Department of Entrepreneurship and Innovative Development.
- In 2020 residents of technoparks also took advantage of subsidies for employee training, export of goods and services, engineering, product promotion and other purposes. The total amount of payments to high-tech companies and entrepreneurs amounted to 266 million rubles. These support measures will also continue to operate this year».
The technology patented by Kalibr's tenant allows restoring all functions of the wrist when a portion of the joint bone is removed, for example, due to a tumor or injury in the distal radius. Previous methods of restoring the affected area and replacing the joint with a prosthesis were associated with loss of hand mobility, additional operations to obtain healthy bone from other parts of the skeleton, the need to remove intact areas, or abrasion of the remaining tissue on the implant. In addition, patients may face difficulties after undergoing postoperative rehabilitation, when the joint has to work again and withstand stress. When using traditional methods of prosthetics, dislocations occur during circular movements of the hand due to insufficient allowable rotation, destabilization of the joint due to the lack of binding of bone and soft tissues and unstable position of the implant, rejection of the artificial joint and other problems.
The presence of a large number of side effects and high risks of negative consequences of the operation are associated with a particularly complex structure of the bones in the wrist. Serial products in most cases do not take into account a number of nuances necessary for successful prosthetics.
Bioengineers of ITK Endoprint have developed a method for creating individual endoprostheses, taking into account the patient's anatomical features, based on his computed tomography images. This takes into account the need to ensure comfort and full mobility immediately after the completion of rehabilitation. Designed and clinically approved implants are 3D printed from titanium using a high precision printer.
«An oncologist surgeon from Tomsk contacted us with the idea of developing a new way to solve problems arising when working with the wrist joint. Our specialists supported the idea and were actively involved in the development process. I am happy to announce that several patients have already been operated on and successfully completed rehabilitation», – said Nikolay Krainov, the head of the company.
The radial endoprosthetics system developed by the company is already used in oncology, traumatology and orthopedics. It makes it possible to replace the affected areas and preserve all healthy tissues. The body of the implant follows the shape of a healthy bone and has a porous post, which corresponds to the peculiarities of the structure of the joints of this particular patient. The pin is installed using a tool specially designed for this purpose, which shortens the operation time. Thanks to this method of insertion, fixation does not require the use of screws, and the porous structure allows bone structures to "grow" into the implant over time, making it one piece with the bone. In addition, the developers have created a special liner made of surgical polyethylene, which precisely follows the cartilaginous surface and eliminates abrasion of the cartilage, giving the joint the ability to rotate stably. The holes provided in the liner for fixing the ligaments are involved in maintaining the stability of the joint after arthroplasty. Also part of the system are fitting models that allow the doctor to plan the operation in advance and prepare in detail for it.
With such a system, operations have already been carried out for a group of patients. All operations were successful, patients were discharged from the hospital and are undergoing a rehabilitation period.
In total, more than two thousand companies work at the sites of the capital's technoparks, over 67 thousand highly paid jobs have been created. The number of technoparks in the capital reached 42 by the beginning of 2021, including 37 operating and five in the status of priority investment projects for their creation..